Project "Evaluation of the antimicrobial activity of selected European fungal species of the genus Phellinus s.l. and their potential use in the treatment of infections caused by bacterial strains with multidrug resistance" is performed within the VIA CARPATIA Polytechnic Network ointhe name of the President of the Republic of Poland Lech Kaczyński. The project manager Lidia Buda-Ożóg, BEng, PhD, DSc, Assoc. Prof. from Department of Building Structures at The Faculty of Civil and Environmental Engineering and Architecture of the Rzeszów University of Technology. The research project is carried out by a cooperation of three research groups: research team from the Białystok University of Technology, the Lublin University of Technology and the Rzeszów University of Technology. The project leader is the Rzeszów University of Technology.
Research team
Bialystok Technical University: Principal Investigator: Mirosław Broniewicz, BEng, PhD, DSc, Assoc. Prof., Research team members: Krzysztof Czech, BEng, PhD, Robert Stachniewicz, BEng, PhD, Filip Broniewicz, BEng, MSc., (PhD student)
Lublin University of Technology: Principal Investigator: Anna Halicka, BEng, Arch., PhD, DSc, ProfTit., Research team members: Łukasz Jabłoński, BEng, PhD
Rzeszow University of Technology: Principal Investigator: Lidia Buda-Ożóg, BEng, PhD, DSc, Assoc. Prof., Research team members: Joanna Zięba, BEng, PhD, Michał Jurek, BEng, PhD, Damian Nykiel, BEng, MSc
Project description
Wind turbines are one of the more popular green sources of electricity that have been used around the world for years. The standard lifetime of wind turbines is 20-25 years, after which time they become waste. WindEurope estimates that around 14 000 wind turbines could be decommissioned by 2023, corresponding to a mass of 40 000 - 60 000 tonnes. According to Barlow’s research, globally the mass of all propellers to be decommissioned by 2050 could be as high as 43 million tonnes. Data on the scale of the wind turbine waste problem, estimated waste volumes, legislation and standards that define the value chain processes and the technical processes that transform it into new valuable materials, have been widely presented in numerous publications. Assessments, initiatives and research on the reuse of wind turbine blades are carried out by projects and consortia such as IEA Wind Task 45,EoLO-HUBs, Lichenblades and Re-Wind, among others. Also, several wind turbine propeller manufacturers have joined forces with recycling companies and building material manufacturers to transform decommissioned propellers into useful products. Such recycling agreements between Veolia and GE Renewable Energy in Germany, Switzerland, Spain and other European countries aim to develop ways to reuse or recycle propellers for construction and building components. The material from which propellers are made varies from manufacturer to manufacturer, typically 80-90% by weight is composite material. Between 60-70% of the mass of the composite is made up of reinforcing fibres - mainly glass fibre and sometimes carbon fibre. The polymer resin binds the fibres into a stiff and relatively lightweight solid matrix. The resins used in wind turbine propellers are most often thermosetting and, during curing, form highly cross-linked polymers that lock the reinforcing fibres in place. Therefore, the proper disposal of composite wind turbine blade fragments is one of the most challenging aspects due to the size of the components, the complexity of recycling and the low market value. Currently, researchers are trying to develop efficient methods to separate the resin from the fibres in order to give the small pieces new life as pellets or slabs. Some of the blades are burned in kilns creating cement or in power plants, but their energy value is low and uneven, and the burnt fibreglass emits pollutants. The requirements for materials used in wind turbine blades, the loads they should meet and an overview of the available materials are presented in many scientific papers.
The Re-Wind Network consortium consisting of five academic institutions - Georgia Institute of Technology, University College Cork, Queen’s University Belfast, City University of New York and Munster Technological University – has developed a catalogue of the use of decommissioned blades for floating platforms, bridge and footbridge construction and lighting poles. The solutions presented here use scans of five decommissioned wind turbine blades. These are an LM blade, a blade from a Vestas turbine, a blade from a General Electric turbine, a blade from a Liberty Clipper turbine and a blade from a Siemens Gamesa turbine. The Decom Tools project, which started in 2018 and focuses on the decommissioning phase of offshore wind farms, presented three concepts for the reuse of wind blades, these are: cement-furnace, pyrolysis and repurposing. The authors of the report point out that while the use of blades in cement and pyrolysis is already quite well recognised scientifically and used in practice, repurposing has few real-world applications. Most of the work presented in the report relates to preliminary designs and visualisations of landscaping structures and the repurposing of blades for sound barrier construction.
Danish company Miljøskærm has come up with an innovative use for decommissioned wind turbine propellers by converting the material from which they are made into noise barriers. Miljøskærm shreds the composite material into small fibres, which are then compressed into sheets, creating highly porous and therefore effective noise barriers. Screens made of such elements have been tested for noise pollution control in the suburbs of Copenhagen, effectively reducing noise levels from 61 to 54 dB. In addition, a life-cycle analysis showed that the use of fibreglass to make acoustic screens resulted in a 60% reduction in CO2 emissions and a 40% reduction in energy consumption during the manufacturing process compared to screens made of aluminium and mineral wool. In Poland, the issue of repurposing was taken up by Andrzej Adamcio, Beng, MSc., from ANMET company. The company uses the robust wind turbine blades to manufacture outdoor furniture and footbridges and bridges. The result of ANMET’s collaboration with the Rzeszów University of Technology was the construction of a footbridge made of LM-type wind turbine blades on the Szprotawa River. Research work preceding the construction of the footbridge was conducted at the Rzeszów University of Technology under the direction of Tomasz Siwowski, BEng, PhD, DSc, ProfTit. The result of the cooperation established with ANMET is three concepts for the use of used wind turbine blades in engineering structures, which are the subject of the proposed project. The first concept involves the use of elements from LM-type and Vestas-type wind turbine blades for the manufacture of walls and Vestas wind turbine blades for the construction of slope protection walls and trenches. Concept two involves the possibility of using fittings obtained from wind turbine blades to make intermediate foundations for buildings and low retaining walls. Concept three, on the other hand, develops noise barriers using components obtained from wind turbine blades. All concepts for the secondary use of wind turbine blades in engineering structures share the same material obtained from the wind turbine blades, analogous problems to be solved in the process of joining the elements and the possibility of mutual application of the solutions developed in concept 2, for the foundation of engineering structures.
Division of the project into phases and issues to be developed within each concept
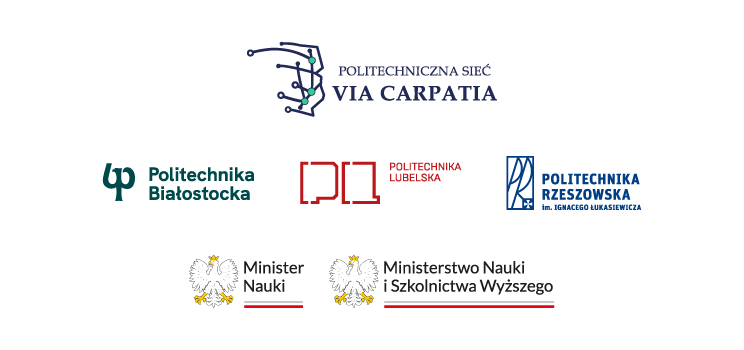